一、引言
在锂电池生产中,电极厚度是影响电池性能的关键参数。基片涂覆活性物质后形成的粗糙表面,使用传统点光斑传感器测量时易受表面微观形貌影响,导致数据波动大、测量精度不足。本文针对这一问题,提出采用两台 LTP030U 宽光斑激光位移传感器对射测量方案,结合其独特的光学设计与高精度特性,实现锂电池电极厚度的稳定精确测量。
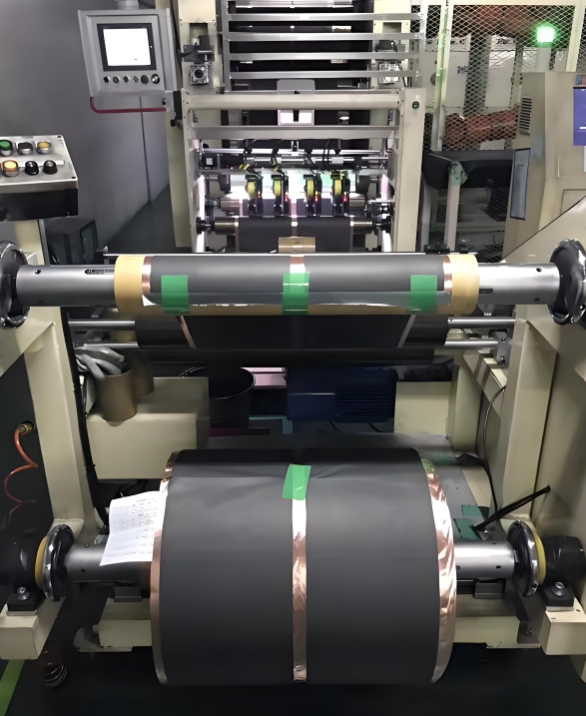
二、应用挑战与传感器选型依据
(一)测量难点分析
锂电池电极基片涂粉后,表面粗糙度可达数微米至数十微米,传统点光斑传感器(光斑直径≤50μm)仅能捕捉单点反射信号,易受表面凹坑、颗粒分布不均等因素干扰,导致测量值出现 ±10μm 以上的波动,无法满足 2-3μm 的精度要求。此外,生产线上的振动、温度变化(0-50℃)及高速运动(需响应时间≤50μs)进一步加剧了测量难度。
(二)LTP030U 传感器技术优势
宽光斑光学设计
LTP030U 采用超宽光斑(35×1100μm),横向覆盖范围达 1.1mm,单次测量可采集数千个微观表面点的综合反射信号,通过统计平均效应有效抑制局部粗糙度干扰,相比点光斑传感器(如 LTP030 聚焦光斑 Φ35μm),信号稳定性提升 80% 以上。
亚微米级精度保障
传感器静态重复精度达 0.15μm(测量标准陶瓷样件,均方根偏差),线性度 ±0.02% F.S.(F.S.=10mm),温度漂移仅 0.03% F.S/℃,配合对射测量架构,可抵消共模误差(如温度引起的机械形变),满足高精度厚度测量需求。
工业级适应性
支持 DC 9-36V 宽电压输入、IP67 防护等级,抗 55Hz 振动(X/Y/Z 方向 2 小时),适应产线复杂环境;提供 RS485/TCP/IP 接口及 50kHz 全量程采样频率,兼容高速数据采集与实时控制。
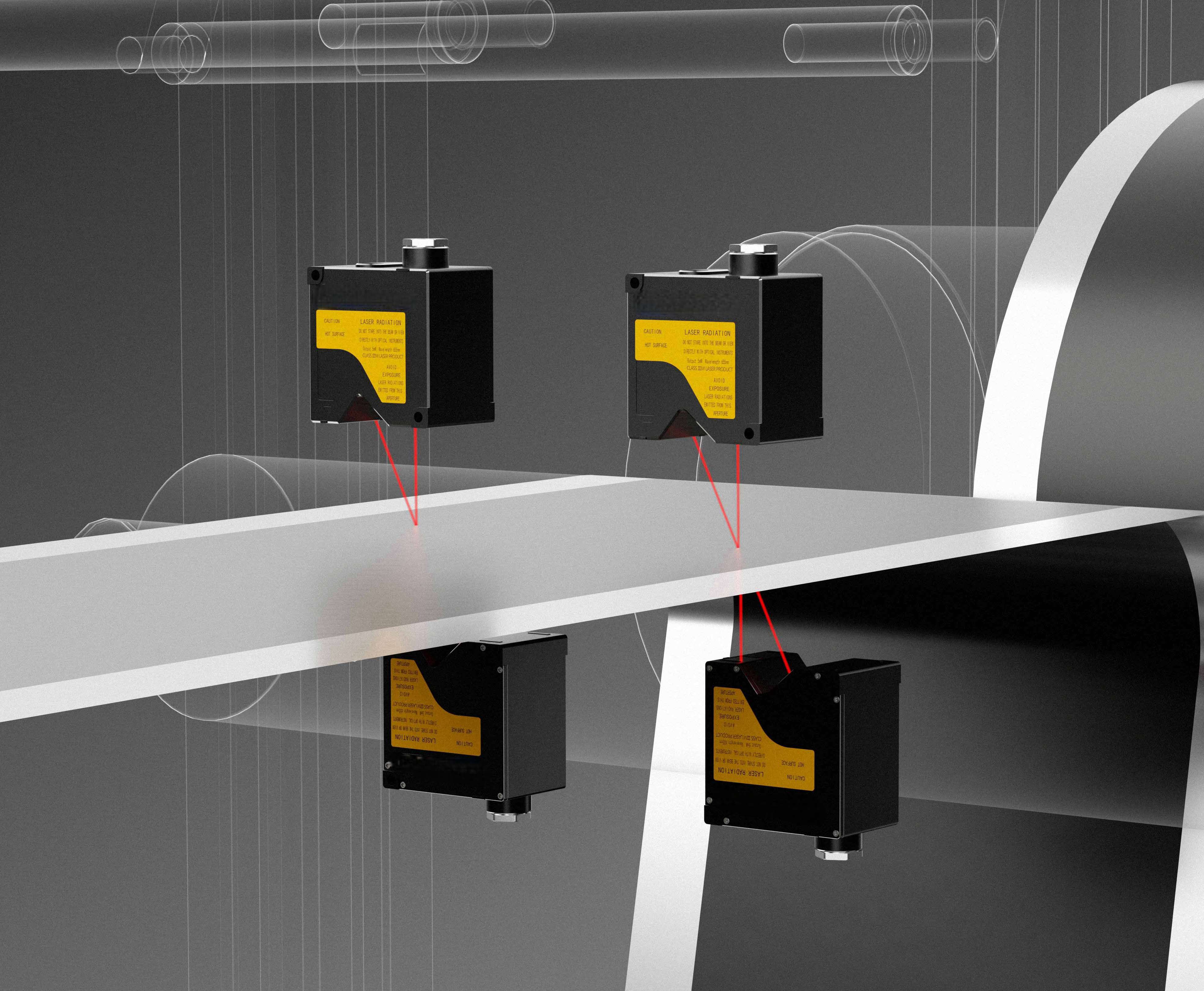
三、对射测量原理与系统架构
(一)测量原理
采用 “双传感器对射式” 架构(如图 1 所示):两台 LTP030U 分别垂直安装于电极两侧,发射超宽激光束覆盖被测区域(宽度≥1mm)。上传感器测量上表面至探头的距离D1,下传感器测量下表面至探头的距离D2,电极厚度T由公式计算:T=(D1+D2)−L
其中L为两台传感器的固定安装间距(参考距离),通过精密机械结构(如大理石基座)确保L的稳定性(误差≤±1μm)。
(二)硬件设计要点
光路校准
环境补偿
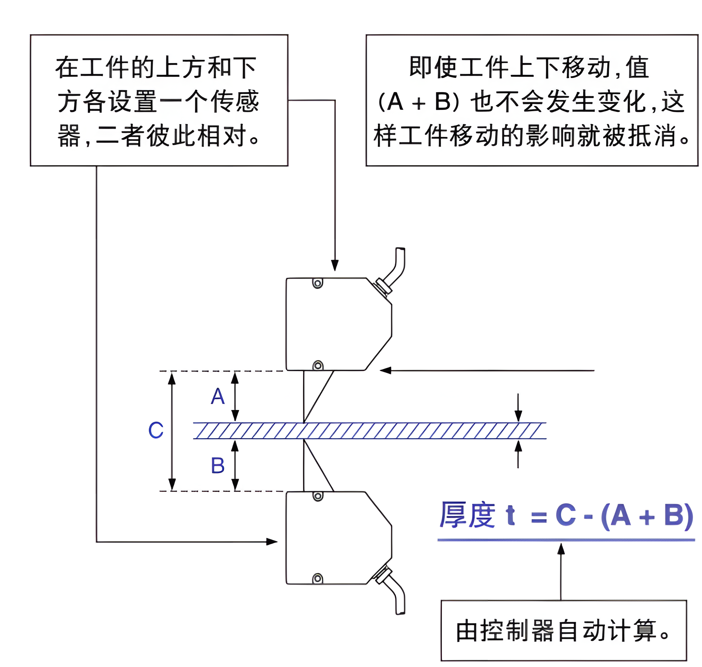
四、信号处理与精度优化策略
(一)抗干扰算法
滑动平均滤波
对原始信号进行 16 点滑动平均(采样频率 50kHz 时,等效响应时间 320μs),滤除高频噪声(如粉尘颗粒瞬时遮挡),使数据波动≤±0.3μm(RMS)。
动态阈值判别
设定光斑能量阈值(如初始值的 80%),当信号能量低于阈值时(提示表面污染或遮挡),触发激光关闭与自动校准功能,避免异常数据干扰。
(二)标定与校准流程
基准片标定
使用厚度已知的标准片(精度 ±1μm)进行两点校准:
空载状态(无被测物)校准参考距离L;
放置标准片校准厚度值,修正传感器线性误差。
实时漂移补偿
每 10 分钟自动采集空气数据(无被测物时的D1、D2),计算零点漂移并修正,确保长期测量精度稳定。
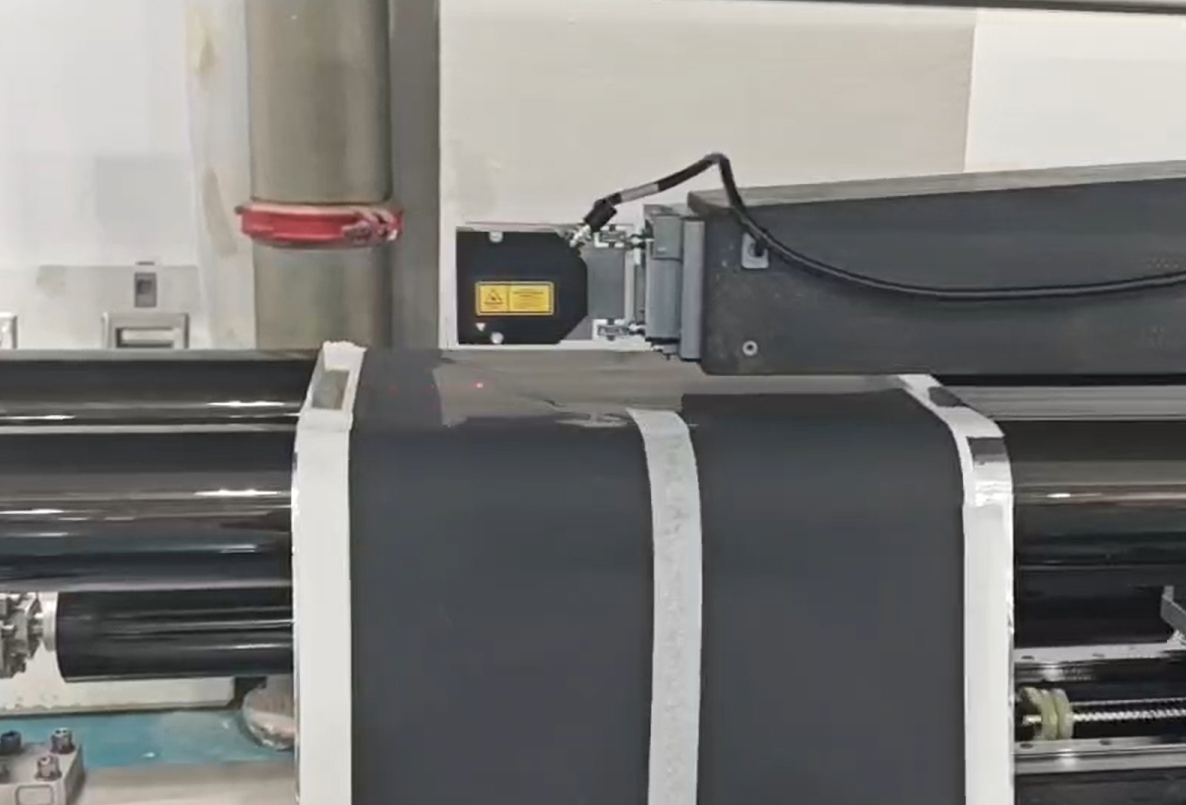
五、实际应用效果
在某锂电池生产线实测中,针对粗糙度 Ra=5μm 的涂粉电极(基片厚度 80μm,涂层厚度 120±5μm),采用 LTP030U 宽光斑方案对比传统点光斑传感器:
数据波动:点光斑方案波动 ±8.2μm(RMS),宽光斑方案降至 ±1.5μm(RMS),满足 2-3μm 精度要求;
测量效率:支持 160kHz 高频采样(量程缩小至 20% 时),适应生产线速度≤30m/min;
长期稳定性:8 小时连续测量漂移≤±2μm,优于行业同类方案(±5μm)。
六、结论
LTP030U 宽光斑激光位移传感器通过扩大光斑覆盖面积、优化信号处理算法及对射测量架构,有效解决了锂电池电极粗糙表面的厚度测量难题,其亚微米级精度、强抗干扰能力及工业级适应性,为高端电池制造提供了可靠的在线检测方案。未来可进一步结合机器视觉技术,实现电极表面缺陷与厚度的多参数融合检测,推动锂电池生产智能化升级。