加工对象:钛合金 TC4 机匣(直径 350mm,叶片型面曲率半径 20-100mm,加工余量 0.3-0.5mm)
核心难点:薄壁结构(最小壁厚 1.5mm)易变形,型面复杂导致定位误差敏感(设计公差 ±0.02mm,表面粗糙度 Ra≤0.2μm)。
硬件系统
测量单元:KUKA KR600 R2830 机器人搭载 LTP150 激光位移传感器(量程 ±40mm,重复精度 1.2μm),采用螺旋线扫描路径(层间距 0.5mm,采样点密度 1 点 /°)。
定位工装:三工位旋转工作台(定位精度 ±5″),配置伺服驱动定位夹紧滑块(行程 ±20mm,分辨率 1μm),通过 120° 对称分布实现径向(X/Y 轴)和角向(θ 轴)解耦调整。
软件算法
偏差计算:基于 Kasa 迭代法拟合圆周 72 个等分点,径向定位精度 ±15μm;通过定位销块切线测量,角向偏差检测精度 ±0.001°。
闭环控制:自动调整滑块补偿径向偏差,角向误差通过修正加工程序角度实现补偿,单次定位周期≤3 分钟。
精度突破:径向尺寸偏差从 ±0.3mm 降至 ±15μm,表面粗糙度 Ra 从 1.2μm 降至 0.15μm,满足航空级精度要求。
效率提升:单工件加工时间从 8 小时缩短至 5.5 小时,良率从 85% 提升至 98%,避免人工对刀的耗时误差。
柔性适配:通过参数化配置,兼容 3 种不同型号机匣,换型时间≤10 分钟,适应多品种小批量生产。
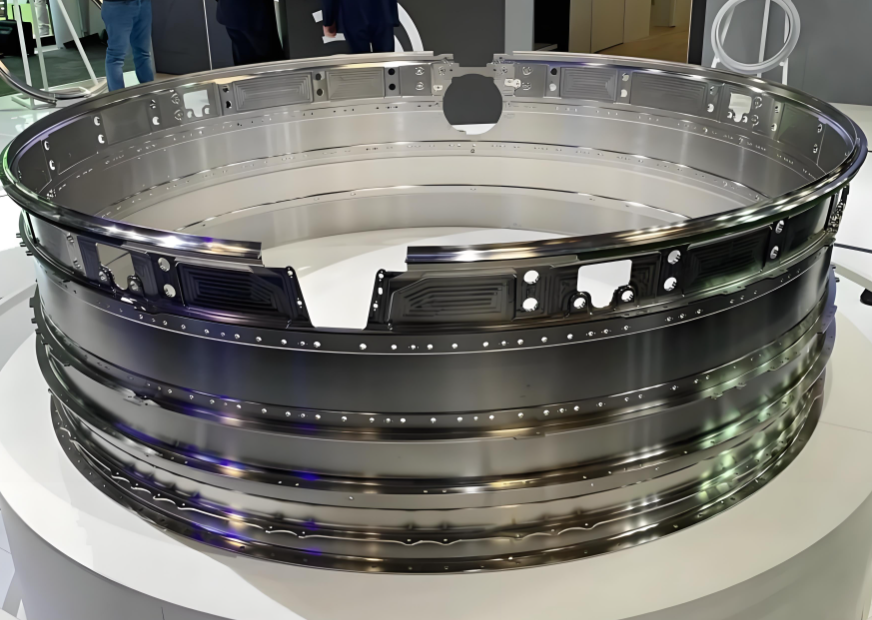
加工对象:镍基高温合金涡轮叶盘(直径 400mm,叶片高度 80mm,叶间流道最小宽度 15mm)
核心难点:叶片型面扭曲度大(最大曲率变化率 0.05mm⁻¹),定位误差易导致打磨过切或欠切。
系统集成
测量模块:采用自主研发的激光位移测量系统(基于三角测量法,线性度 ±0.02% F.S.),机器人末端集成快换装置,支持传感器与砂带机工具头(接触力控制 ±5N)自动切换。
定位策略:通过三滑块机构调整工件圆心,结合角向偏差补偿(公式 φ=λ/R),实现定位精度 ±15μm(径向)和 ±0.001°(角向)。
工艺优化
路径规划:针对叶间流道设计五轴联动轨迹,刀轴矢量与型面法向夹角控制在 15° 以内,避免干涉;砂带线速度 800mm/s,接触压力 30N(力传感器实时反馈调整)。
误差补偿:基于测量数据实时修正机器人 TCP(工具中心点),补偿机械臂运动误差(重复定位精度从 ±0.08mm 提升至 ±0.02mm)。
质量提升:叶片缘板厚度偏差从 ±0.1mm 降至 ±0.01mm,流道表面粗糙度 Ra≤0.18μm,通过航空发动机热疲劳测试(循环次数≥10⁴次无裂纹)。
成本节约:减少人工检测工序(每工件检测时间从 2 小时降至 15 分钟),年节约成本约 300 万元(按年产 500 件计算)。
技术创新:实现 “测量 - 定位 - 打磨 - 检测” 全流程自动化,获国防科技进步三等奖。
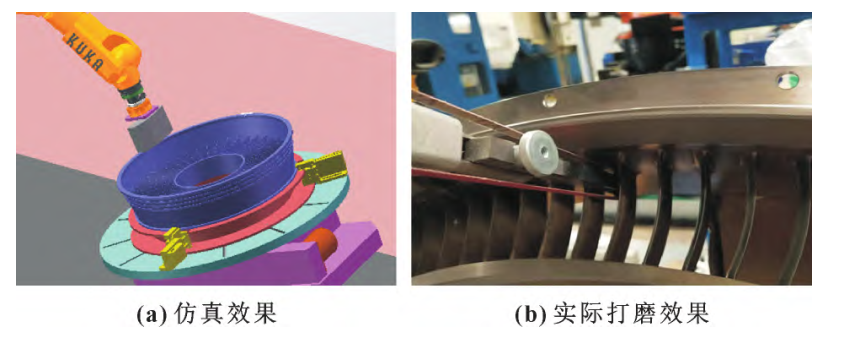
加工对象:碳纤维复合材料螺旋桨叶片(长度 2.5m,叶面扭曲度 ±10°,表面精度要求 ±0.05mm)
核心难点:柔性材料易变形,传统接触式测量易损伤表面,需高精度非接触定位。
设备配置
测量系统:集成激光位移传感器(三角法,精度 ±20μm)与视觉相机,构建多传感器融合系统,获取叶片点云数据(采样密度 0.5mm),通过 RoboDK 软件实现点云与 CAD 模型的高精度配准(配准误差≤0.03mm)。
打磨单元:KUKA 机器人搭载轨道砂光机(振幅 2mm,频率 50Hz),集成 ATI 力传感器(力控制精度 ±1N),实现恒压力抛光(压力设定 25N)。
关键技术
位姿匹配:通过叶片榫头定位销块的激光测量,计算角向偏差并补偿至机器人运动轨迹,确保叶背与叶盆的抛光轨迹与理论型面偏差≤±0.04mm。
路径优化:采用等参数线法生成抛光轨迹,针对叶面曲率变化自动调整砂带接触角度(最小曲率半径处步长 0.3mm),避免抛光纹路不均。
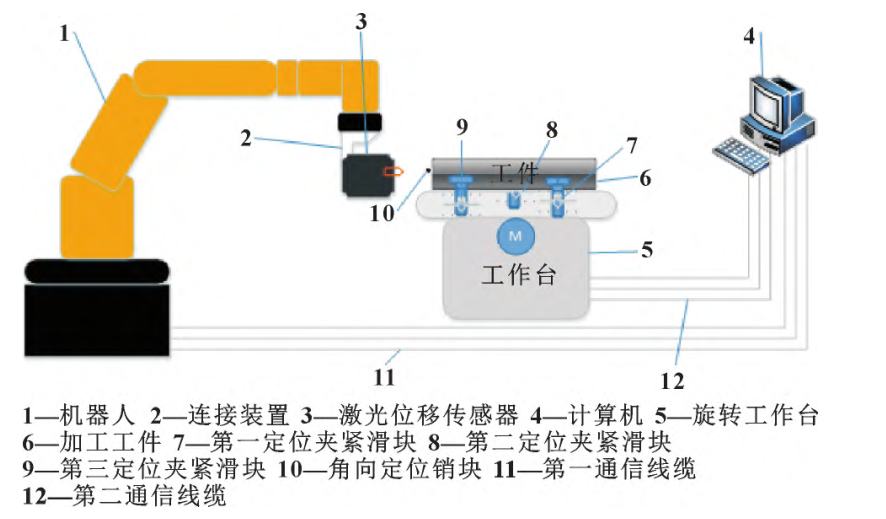
表面质量:抛光后叶面粗糙度 Ra≤0.1μm,气动性能测试显示阻力系数降低 3%,达到航空级镜面标准。
效率对比:单叶片加工时间从人工操作的 12 小时缩短至 4 小时,且消除了人工抛光的厚度不均问题(最大厚度偏差从 ±0.2mm 降至 ±0.06mm)。
安全性:非接触测量避免叶片损伤,力控制技术防止过载导致的材料分层,缺陷率从 5% 降至 0.5% 以下。
加工对象:铝合金蒙皮壁板(尺寸 3m×2m,曲率半径 500-2000mm,边缘精度要求 ±0.1mm)
核心难点:大尺寸薄壁件定位基准易漂移,传统机械定位耗时且精度不足。
定位系统
激光测量网络:在机器人末端安装 3 组 LTP150 传感器(呈 60° 分布),同时扫描壁板边缘特征点(每米采集 50 个点),通过最小二乘法拟合边缘曲线,确定工件实际位置与理论坐标系的偏差(X/Y 轴 ±20μm,θ 轴 ±0.002°)。
动态调整:驱动真空吸附工装的三自由度调整机构(平移 ±5mm,旋转 ±0.5°),基于测量数据实时补偿壁板安装偏差。
加工工艺
铣削策略:采用 “先测量后加工” 模式,根据实时定位数据生成铣削路径,主轴转速 8000rpm,进给速度 500mm/min,刀具选用金刚石涂层立铣刀(直径 10mm,刃长 15mm)。
误差补偿:通过机器人运动学模型修正 TCP 位置,补偿机械臂热变形(温度每变化 10℃,补偿量≤±0.05mm)。
边缘精度:铣削后边缘直线度误差≤±0.08mm,轮廓度误差≤±0.1mm,满足大部件装配间隙≤0.2mm 的要求。
生产效率:单壁板定位时间从 30 分钟缩短至 5 分钟,铣削效率提升 40%,年产能从 2000 件提升至 3500 件。
标准化应用:形成一套适用于大尺寸曲面件的定位加工流程,已推广至 3 种型号飞机蒙皮生产。
核心技术共性
非接触测量:激光位移传感器实现微米级精度的径向 / 角向偏差检测,避免接触式测量的工件损伤与耗时问题。
闭环控制:通过 “测量 - 计算 - 调整 - 加工” 全流程自动化,将定位误差抑制在设计公差 1/10 以内(如 ±15μm≤±0.02mm 的 1/1.3)。
多学科融合:集成机器人运动学、曲面拟合算法、力控制技术,解决复杂曲面加工的干涉、变形等难题。
行业推广价值
精度对标:达到国际先进水平(如美国 AeroGlide 系统径向精度 ±20μm,本案例 ±15μm),打破国外技术垄断。
成本效益:单套系统投资回收期≤2 年(按年节约人工 / 返工成本计算),适用于航空航天、光学器件等高端制造领域。
标准化意义:建立复杂曲面工件的自动化定位加工标准,推动行业从 “经验驱动” 向 “数据驱动” 转型。
上述案例表明,基于激光位移测量的机器人自动定位打磨系统在航空复杂曲面加工中已实现工程化应用,核心在于通过高精度测量、智能算法与精密工装的深度融合,解决了传统加工中的定位难、精度低、效率差等问题。未来随着多传感器融合、数字孪生等技术的发展,该类系统将进一步向智能化、柔性化方向升级,成为高端装备制造的核心技术支撑。